Dentro la fabbrica italiana che realizza gli occhiali LVMH
Inside the Italian factory that makes LVMH glasses
Con la sua facciata in vetro all’avanguardia e acciaio color rame, la manifattura di Thélios a Longarone, nella regione veneta dell’Italia, prende in prestito i materiali dalle montature degli occhiali prodotti al suo interno. Ma mentre l’atmosfera è industriale, l’edificio assomiglia più a una galleria d’arte contemporanea che a un’installazione manifatturiera. (Lo sfondo pittoresco delle Dolomiti contribuisce ulteriormente a questo effetto.)
LVMH ha creato Thélios nel 2017 per prendere il controllo degli occhiali delle sue maison, precedentemente prodotti su licenza. Ha inaugurato l’impianto di Longarone un anno dopo con l’obiettivo di portare tutto – design, produzione, distribuzione, il pacchetto completo – in-house. Lo spazio di 20.000 metri quadrati produce occhiali da sole per i marchi del Gruppo LVMH, tra cui Dior, Loewe, Celine, Fendi, Fred e, a partire dal prossimo anno, Bulgari. Ha una capacità annuale di circa 4,5 milioni di montature per occhiali e impiega 1.000 persone. Se hai seguito il guardaroba del tour Renaissance di Beyoncé, questo è il luogo responsabile degli occhiali Giv Cut di Givenchy con influenze fantascientifiche, che l’artista ha indossato in varie combinazioni – non da ultimo quelle versioni stampate in 3D, personalizzate con cristalli.
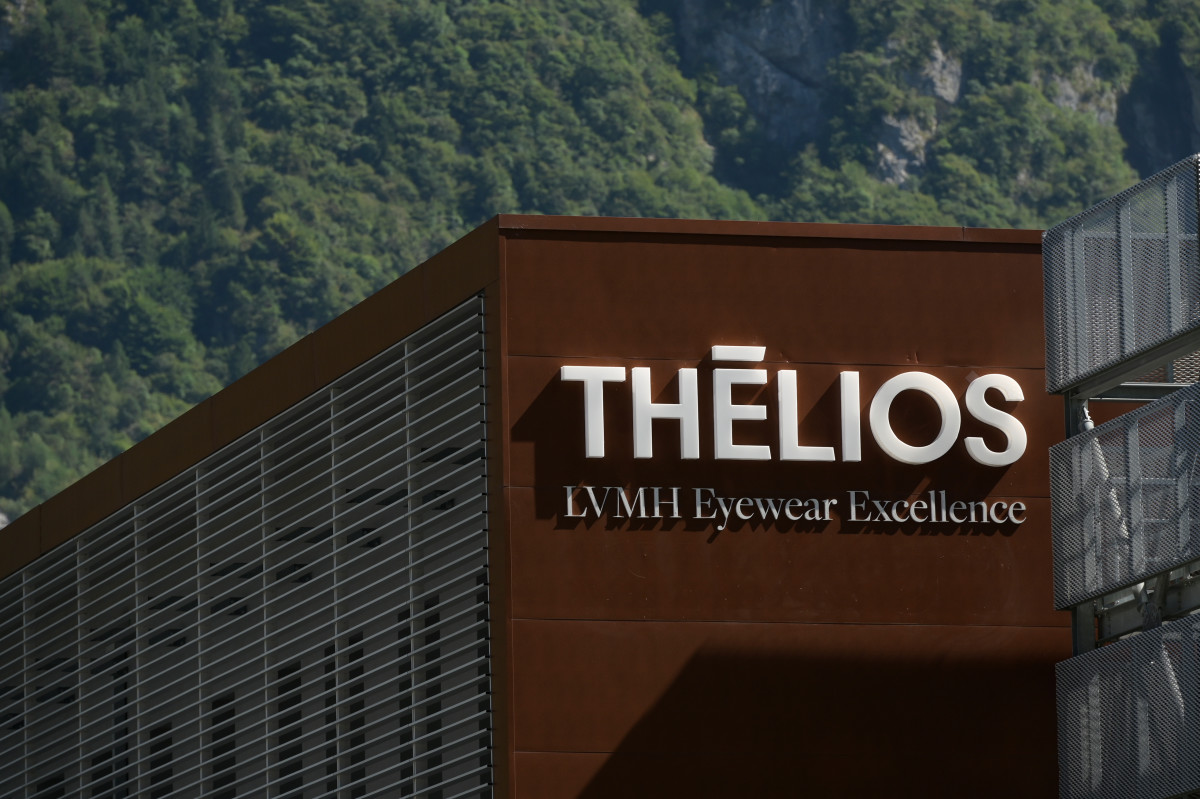
Manifattura Thélios a Longarone.
Foto: Stefanie Rex/Cortesia di Thélios
Come per la bellezza, gli occhiali da sole svolgono un ruolo importante come primo prodotto di accesso per i clienti di lusso. Come afferma il CEO Alessandro Zanardo a HotQueen, l’obiettivo di Thélios era elevare questa categoria, garantendo che riflettesse e rappresentasse i marchi di lusso LVMH in termini di qualità e creatività. “Se vuoi avere un prodotto eccellente, in un tempo affidabile, in linea con il resto di ogni collezione, devi avere un controllo diretto”, afferma.
- Sofia Richie giura su questo marchio di trucco, quindi l’ho m...
- Gli acquirenti riferiscono di avere ciglia ‘più lunghe e più ...
- Un look #PSL Pumpkin Spice (lo chiamo Pumpkin Spice Jewels), e inch...
Thélios voleva che la manifattura fosse “il luogo in cui si concentrava la migliore competenza per la categoria: i migliori designer, prototipisti, tecnici che possiamo trovare”, aggiunge Zanardo. “Il risultato finale non deve avere compromessi”.
Per garantire un’allineamento totale in termini di identità creativa e di marca, continua, “deve esserci una vera partnership e un dialogo costante con ciascuna casa rispettiva, lavorando insieme per tradurre il briefing di design in qualcosa che possa essere prodotto industrialmente”.
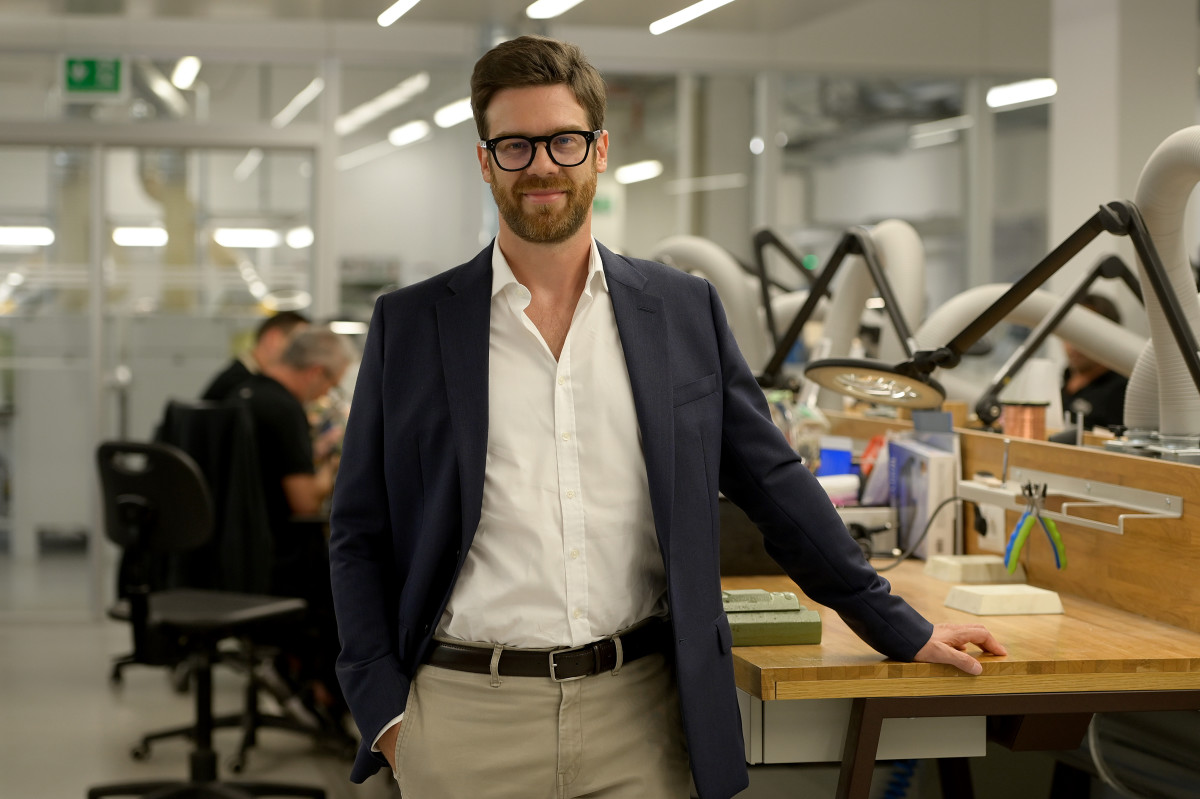
Alessandro Zanardo.
Foto: Stefanie Rex/Cortesia di Thélios
Un esempio di ciò potrebbero essere gli occhiali gonfi Inflated di Loewe, il cui concetto è stato tratto dalle calzature a palloncino surrealisti della collezione Primavera 2023 di Jonathan Anderson. Il percorso inizia nel dipartimento di prototipazione della manifattura, dove i design vengono prima resi digitalmente utilizzando software CAD. I file grezzi “possono anche essere utilizzati per creare risorse digitali che supportano il lancio dei prodotti fisici”, afferma il responsabile della pianta di prototipazione Enrico Cori, dimostrando su un touchscreen gigante.
Il passo successivo è la creazione di prototipi fisici dai file digitali. Ogni parte della montatura viene realizzata utilizzando una macchina diversa specializzata in un processo diverso e utilizza un programma diverso: una macchina taglia le montature, un’altra taglia le aste (il termine tecnico è “tempi”), un’altra inserisce filo nell’acetato in modo che mantenga la sua forma (che comporta il riscaldamento dei tempi a 200 gradi e quindi la loro fissazione riducendo improvvisamente la temperatura). Questo richiede tra le otto e le 20 ore per essere completato.
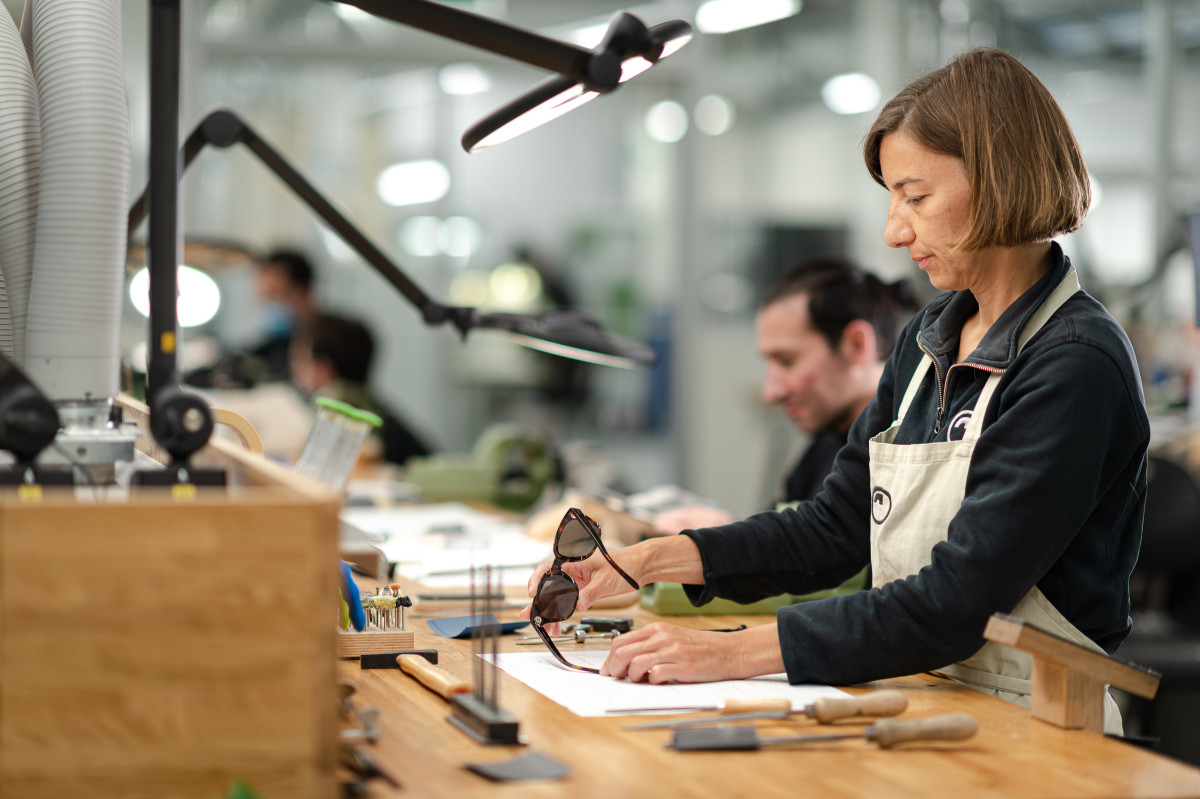
Prototipazione presso Thélios.
Foto: Giovanni Samarini/Cortesia di Thélios
Una volta terminato il prototipo, vengono creati 20 pezzi per ciascun modello in ogni colore nell’area di industrializzazione, per garantire che possano essere prodotti con successo su larga scala senza intoppi. Poi viene la produzione, effettuata utilizzando versioni industrializzate delle macchine di prototipazione, che sono allineate in falangi su vaste superfici di fabbrica; alcune sono programmate per funzionare 24 ore su 24, 7 giorni su 7.
Ogni montatura coinvolge più di 80 processi diversi. C’è una macchina per lucidare le montature dall’acetato grezzo a un brillante lucido, che le fa rotolare con una serie di diverse dimensioni di trucioli di legno. “È come una lavatrice”, dice Cori. “Ruota i trucioli e i pezzi di legno colpiscono l’acetato per rendere la superficie lucida. È necessario impostare diversi tempi per ogni fase di ogni montatura.”
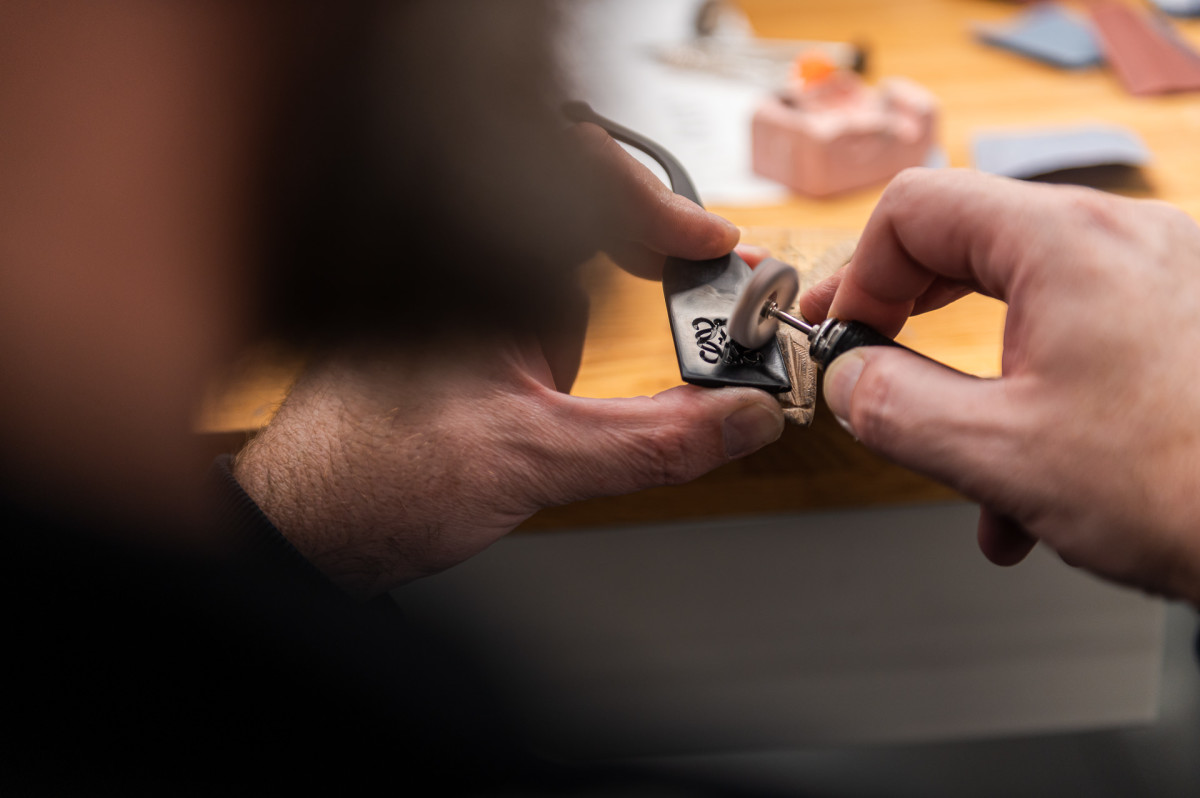
Un artigiano al lavoro su un paio di occhiali da sole Loewe.
Foto: Giovanni Samarini/Cortesia di Thélios
Alcuni passaggi sono eseguiti da artigiani esperti che seguono due anni di formazione presso Thélios. Ad esempio, i piccoli loghi metallici su alcune montature Celine e Dior devono essere applicati con pazienza a mano in modo che si adattino perfettamente alle minuscole lettere incise a laser sulle aste stesse. “Devono essere posizionati parallelamente alla montatura con l’angolazione corretta”, spiega Cori. “È necessario fare molta attenzione per evitare bolle o polvere.”
Le lenti sono l’unico elemento degli occhiali non prodotto internamente. Tuttavia, vengono adattate e rifinite nella manifattura. (Ad esempio, il logo sulle lenti delle montature oversize Fendi Baguette viene realizzato mascherando parti della superficie con uno stencil e poi spruzzandole con ossido metallico vaporizzato.)
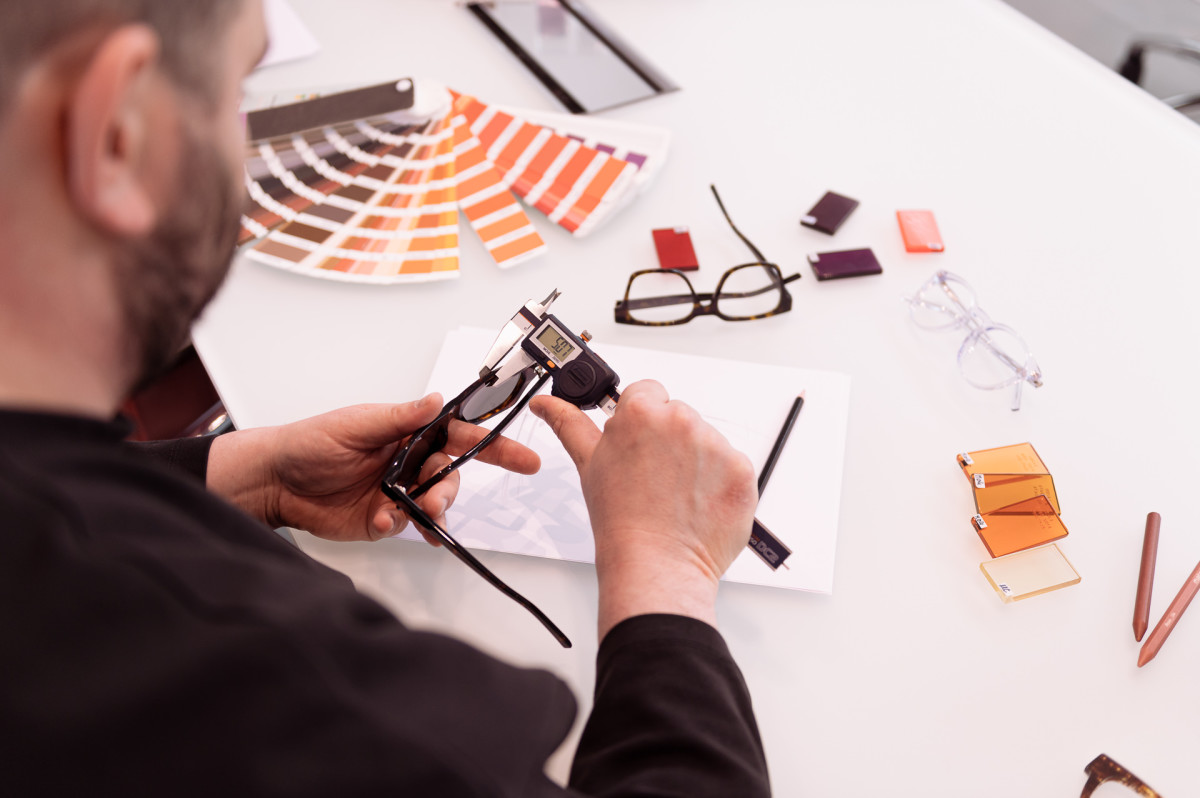
Dettagli finali.
Foto: Giovanni Samarin/Cortesia di Thélios
Le suddette montature 3D stampate Givenchy Giv Cut (e anche il recente modello Shadow di Fendi) vengono prodotte all’interno di una cabina gigante nell’area di prototipazione che assomiglia a una cabina abbronzante e a una funivia di montagna. All’interno si trova una macchina che scalda il componente base in polvere di nylon in strati programmati con precisione, in modo che cambi in solido nelle aree necessarie. Il risultato è un blocco compatto di polvere: “una volta eliminato l’eccesso, si trovano all’interno i pezzi finiti come un fossile”, dice Cori.
Secondo Zanardo, le tecniche di stampa 3D introdotte da Thélios l’anno scorso erano state utilizzate precedentemente nell’industria degli occhiali, ma non negli occhiali di lusso. “Questa è stata l’innovazione, essere in grado di elevare la qualità in modo che potesse essere considerata comparabile ad altre tecniche e materiali utilizzati per gli occhiali di lusso”, dice. Sebbene ammetta che i volumi prodotti non siano vastamente significativi, è convinto che “abbia un enorme impatto strategico” sul business: “Il tempo di commercializzazione è di solito piuttosto lungo nella maggior parte delle categorie di lusso, ma con la stampa 3D è praticamente ‘vedi ora, compra ora’. Questa è la cosa importante.” (Cori aggiunge che la stampa 3D è particolarmente utile per geometrie insolite, perché non si è vincolati da uno stampo.)
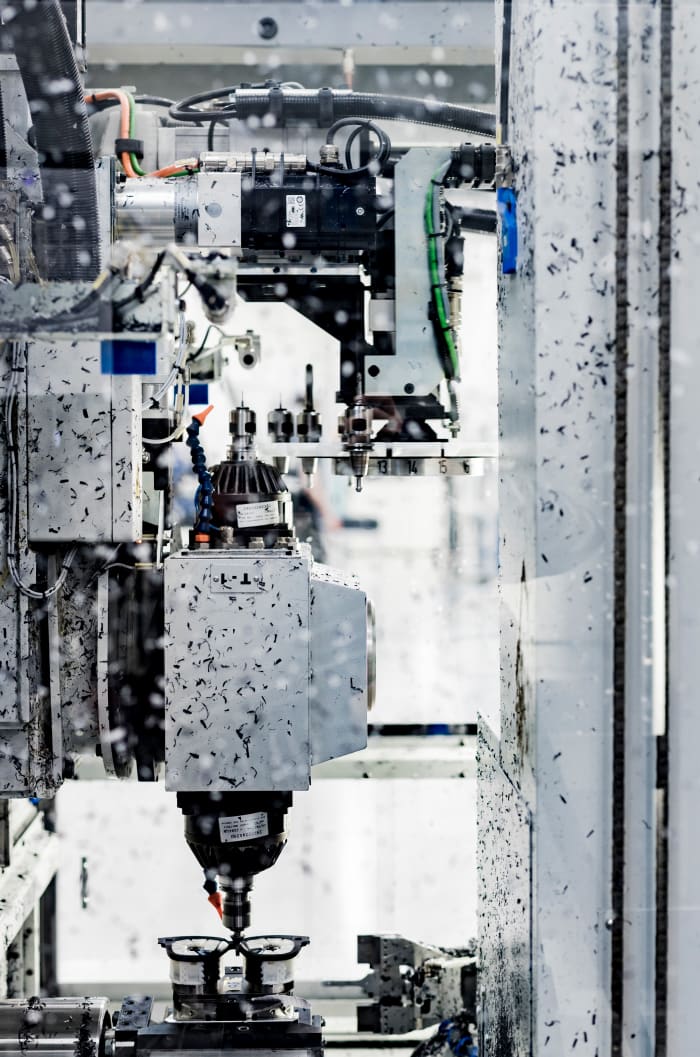
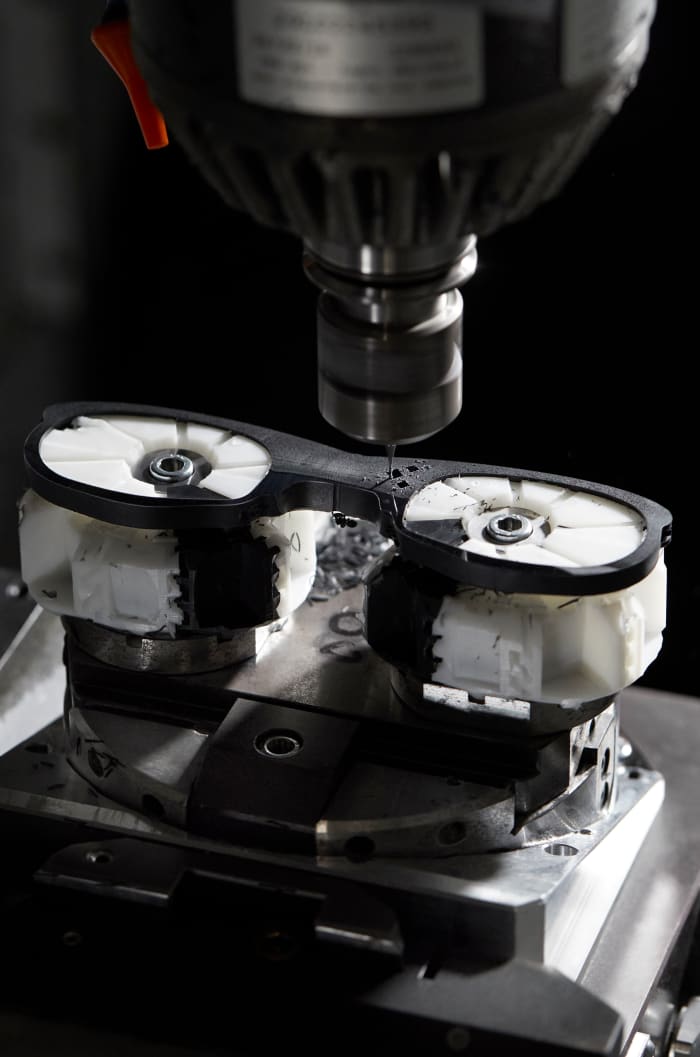
Foto: Ava du Parc/Cortesia di ThéliosFoto: Giovanni Samarini/Cortesia di Thélios
La sostenibilità non è affrontata solo dai 2.529 pannelli solari sul tetto della manifattura, ma anche nei suoi progetti di sviluppo: l’azienda sta lavorando a una nuova versione di acetato che sostituisce alcune delle sostanze chimiche con materiali biologici, ad esempio.
“In passato, i materiali sostenibili erano meno qualitativi, nel senso che avevano uno standard inferiore in termini di prestazioni”, dice Carlo Roni, Direttore di Sviluppo Prodotto e Ricerca e Sviluppo di Thélios. “Stiamo mescolando insieme diversi tipi di materiali per trovare una soluzione”.
All’inizio di questo mese, Thélios ha annunciato l’acquisizione strategica del marchio francese di occhiali da sole per attività all’aria aperta Vuarnet, fondato dallo oculista Roger Pouilloux e dallo sciatore olimpico francese Jean Vuarnet, e che rimane uno dei pochi marchi di occhiali nel mondo occidentale a produrre le proprie lenti minerali. Sebbene il vetro, per definizione, sia una opzione più sostenibile rispetto alla plastica, l’output di Vuarnet è anche noto per le sue capacità di performance, in quanto combina una resistenza e una leggerezza incomparabili.
“Non si tratta di aggiungere sempre più marchi a Thélios”, sostiene Zanardo. “Ce ne sono alcuni sul mercato che hanno una qualità molto alta in termini di eredità, design iconico, know-how o percezione del cliente che li rendono davvero unici.” La capacità di Vuarnet di produrre lenti minerali è stata un fattore determinante: “Siamo felici di integrarla nella nostra struttura industriale e svilupparla.”
Divulgazione: Thélios ha pagato per il viaggio e l’alloggio del giornalista per realizzare questo articolo.